CONTROL VALVES modulate the flows of process or heat-transfer fluids and stabilize variations in material as well as heat balance of commercial processes. They manipulate these flows by altering their openings and modifying the power required for the flow to feed them. Like a control valve closes, pressure differential needed to pass through exactly the same flow increases, and also the flow is reduced. Figure 1 (see below) illustrates the pump curve of the constant-speed pump and also the system curve from the procedure that the pump serves. The elevation (static) mind of the operation is constant, as the friction loss increases with flow. The pressure generated through the pump is the sum system curves (friction and static) and also the pressure differential (ΔP) needed through the control valve. Because the valve throttles, the pump travels on its curve, while delivering the needed valve pressure drop.
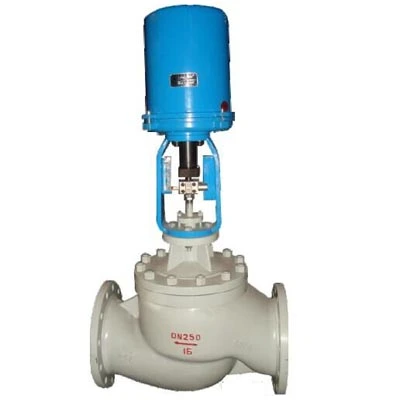
The pumping energy invested to beat the valve differential is wasted energy, and it is the main difference between your pressure needed to "push" (transport) the fluid into the process (system curve, at the bottom left, in Figure 1) and also the pump curve from the constant-speed pump. Pumps are selected to satisfy the utmost possible flow need for the procedure so that they are usually oversized during normal operation. Consequently, using control valves to control the flow generated by constant-speed pumps wastes energy, and increases plant-operation costs.
Therefore, when making a control system, a procedure-control engineer must first decide whether a control valve or perhaps a variable-speed pump should be employed to throttle the flow. Variable-speed pumps reduce flow by reduction of pump speed. So, rather of burning energy unnecessarily created by the pump mind, that energy isn't introduced, to begin with. This lessens operating costs but increases capital investment because variable and constant-speed pumps usually are more expensive than control valves.
When several users are provided through the same variable-speed pump, its speed could be instantly adjusted with a valve-position controller (VPC), which detects the outlet of the very most-open user valve (MOV). The MOV isn't permitted to spread out beyond 80-90% because, once the set-reason for the VPC is arrived at, this integral-only controller starts growing the pump speed. This boosts the available pressure drop for the valves, which reduces their openings.
FIGURE 1:
Pump and System Curves
Available valve pressure drops of
control valves.
Valve Types and Characteristics
When the cost-benefit analysis evaluating constant and variable-speed pumping systems favors using throttling valves, the following task is to decide on the right valve type for that application. Figure 2 (see below) implies that various valve designs have different pressure and temperature ratings, costs, capacities (Cd = Cv/d2), etc. When the valve type is chosen, the following task is to decide on the valve characteristics and size of the valve. These traits determine the connection between valve stroke (control signal received) and also the flow with the valve, while size is dependent upon maximum flow needed.
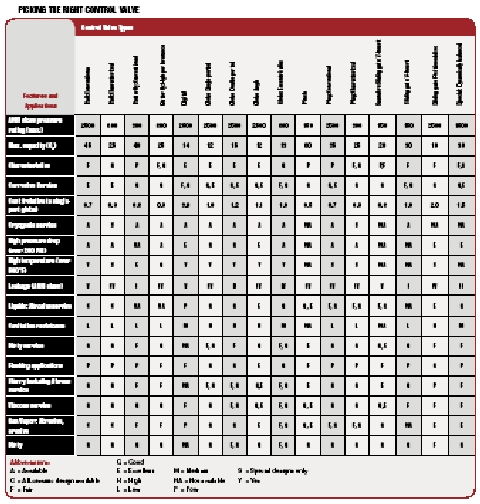
FIGURE 2: Choosing The Right CONTROL VALVE
Control Valve Selection
With regards to selecting and sizing control valves, this excellent and completely non-commercial valve selection chart will not only help you select the best control valve to do the job but additionally works as a fantastic reference tool you are able to download! Click on the chart to spread out an enlarged pdf version for simple viewing, or click on the Download Now button in the finish want to know, in order to save the chart for future reference.
After start-up, when the control loop has a tendency to oscillate at low flows but is sluggish at high flows, users should think about switching the valve trim characteristics from straight line to equal-percentage. Inversely, if oscillation is experienced at high and sluggishness at low flows, the equal-percentage trim ought to be substituted for a straight line one. Altering the valve characteristics may also be done (sometimes easier) by characterizing the control signal resulting in the actuator instead of replacing the valve trim.