A
valve positioner is really a device accustomed to decrease or increase the environment load pressure driving the actuator of the
control valve before the valve‘s stem reaches a situation balanced towards the output signal in the process variable instrument controller.
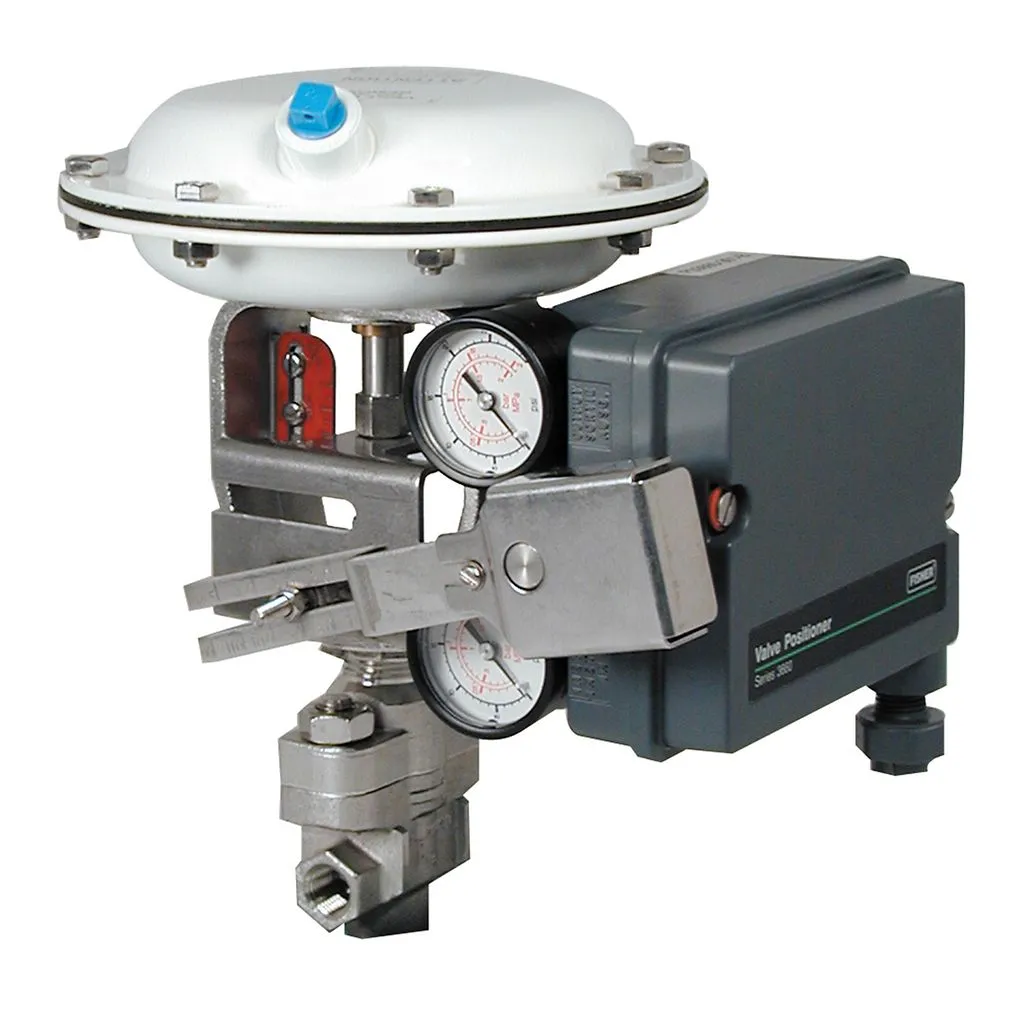
Positioners are usually mounted quietly-yoke or top casing from the pneumatic actuator for straight line-sliding-stem control valves and also at or close to the finish-of-shaft for rotary control valves. For either fundamental design type, the valve positioner is connected robotically towards the valve stem or valve shaft to ensure that their position could be in contrast to the positioning determined through the controller. This mechanical feedback linkage work in a way the process controller informs the positioner to "change" squeeze feedback linkage reports to the positioner confirming that a general change in the positioning of the valve stem has happened and provides a feeling of the magnitude from the alternation in position. Observe that for continuous control of the whole stroke from the valve, using positioners is generally necessary when the valve position is needed to carefully stick to the control signal.
Positioners are usually mounted quietly-yoke or top casing from the pneumatic actuator for straight line-sliding-stem control valves and also at or close to the finish-of-shaft for rotary control valves. For either fundamental design type, the valve positioner is connected robotically towards the valve stem or valve shaft to ensure that their position could be in contrast to the positioning determined through the controller. This mechanical feedback linkage work in a way the process controller informs the positioner to "change" squeeze feedback linkage reports to the positioner confirming that a general change in the positioning of the valve stem has happened and provides a feeling of the magnitude from the alternation in position. Observe that for continuous control of the whole stroke from the valve, using positioners is generally necessary when the valve position is
Causes of Using Valve Positioners
The reason why for utilisation of the valve positioner are summarized below:
(1) Increase control system resolution i.e. fine control
(2) Facilitate operation once the greater number within the actuator bench-set range is more than 15psig. i.e. 10 – 30psig, 6 – 30psig
(3) Permit the employment of characteristic cams in rotary valves
(4) Minimize valve stem packing friction effects and also the resulting hysteresis, designed for hot temperature packing materials for example graphite
(5) Negate flow-caused reactions to greater pressure drops. i.e make amends for internal pressure imbalances
(6) Elevated speed of reaction to a general change in process enables faster loading and venting.
(7) Permit split varying. i.e. one controller for 2
(8) To beat seating friction in rotary valves
(9) Allow distances between controller and control valve
(10) Allow number of flow variation. i.e. operate at under 10% travel under normal conditions
(11) Allow elevated use of 4 - 20mA electronic signal
(12) Permit utilization of piston actuators rich in instrument air supply pressures.
Kinds of Positioners
Positioners can be found in three configurations:
Pneumatic Positioners
A pneumatic signal (usually 3 - 15 psig) is provided towards the positioner. The positioner translates this to some needed valve position and increases the valve actuator using the needed air pressure to maneuver the valve towards the correct position. Observe that the positioners accustomed to articulate the key of valve positioners listed here are pneumatic.
Analog I/P Positioners
This positioner performs exactly the same function as pneumatic type, but uses electrical current (usually 4-20 mA) rather of air because the input signal.
Smart or Digital Positioners
Smart or digital positioners function greatly because the analog I/P type described above, nevertheless it differs for the reason that the electronic signal conversion is digital instead of analog. Digital products cover three groups namely:
(1) Digital Non-Communicating: Within this type, a present signal (4 - 20 mA) is provided towards the positioner, which both forces the electronics and controls the output.
(2) HART : This is equivalent to digital non-communicating but is able to two-way digital communication within the same wires employed for the analog signal.
(3) FieldBus: This kind receives digitally based signals and positions the valve using digital electronic circuitry coupled to mechanical components. Here, an exciting-digital control signal replaces the analog control signal. Furthermore, two-way digital communication can be done within the same wires. Fieldbus technologies help the finish user by enabling improved control architecture, product capacity and reduced wiring.
Typical
Control Valve Configuration Without Positioner:
The diagram above is perfect for a straight line sliding stem control valve with no positioner. The valve comes with an actuator bench group of 5 - 13psig. As possible seen, the valve configuration is air to spread out, fail close (ATO - CFC). When the controller (PIC) outputs a control SIGNAL (designated SIG within the diagram above), the signal functions because the load pressure around the diaphragm actuator from the valve changes, leading to valve stem travel. However, as possible seen in the plot of Diaphragm / SIG Pressure against % percent travel of valve, there's significant hysteresis through the valve stroke largely because of friction and forces of inertia inside the valve. It ought to be noted above the controller signal, SIG and also the LOAD pressure around the actuator are identical flow stream. Actuator air flows with the pneumatic controller and also the interconnecting tubing air is venting with the controller. Because of the lack of a valve positioner, no stem position feedback.
Typical Control Valve Configuration with Positioner
The diagram above is perfect for a straight line sliding stem control valve having a positioner. The valve comes with an actuator bench group of 5 - 13psig. As possible seen, the valve configuration is air to spread out, fail close (ATO - CFC). Here also there's an analog linkage between your valve stem and also the positioner (V/P within the diagram above) supplying stem position feedback towards the positioner. As possible seen above, controller outputs an indication, SIG , which enters the positioner. Having a valve positioner, the SIG and cargo streams are separate. Actuator air flows with the valve positioner and it is short interconnecting LOAD tubing. The pneumatic controller (PIC) air flows with the tubing interconnecting and also the positioner, also known as the SIG tubing.
The valve positioner provides "stem position feedback" towards the control loop for the reason that a general change in controller SIG output forces a general change in positioner LOAD output which leads to a valve stem travel. The mechanical feedback linkage then "confirms" that travel happened. If no travel is given to the positioner, positioner output continuously change until stem travel is confirmed. The plot of positioner output/LOAD versus % valve travel implies that the hysteresis present is extremely less space-consuming than the main one with no valve positioner. Typically valve hysteresis with positioners is 5% of valve stroke.